Ingenjörsdata AB has been engaged in the support (VOLVO Car Corporation) and further development of software components (for LS-DYNA) to enhance the simulation of various metal forming operations: deep drawing, stretch pressing, flanging, hydro formning etc.
As an example it is below shown results from the simulation of the deep drawing of an oil-trough in mild steel (DOMEX 220 YP), on behalf of IUC (Centre of Industrial Research) in Olofström .
The tooling is modelled to great detail e.g. including the description of blank holders and drawbeads, see figure below, that take on rigid material data (to save processing time) whereas the actual blank is described as elasto-plastic with transverse orthotropy (hardening parameter R=2.0). The modelling is to a high degree performed automatically from the CAD-data (VDA format) in the pre-processor of MEDINA . MEDINA has also been used as post-processor.
As a selection from the most vital results, it is below shown, apart from the resulting shape after release from the tooling, the margin to failure measured in the sence of forming limit diagram (FLD ), and also the resulting ralative thickness, i.e. the ratio thickness/original thickness. Fig. 1 Model with die, punch, blank holder and blank.
Fig. 2 Utilisation factor according to FLD.
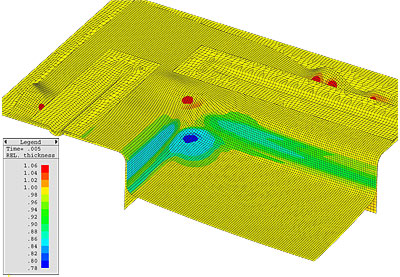
Fig. 3 Resulting relative thickness
Keywords: metal forming, deep drawing, non linear, transverse orthotropy, elasto-plastic, hardening parameter R, FLD, contact, CAD, VDA, LS-DYNA, MEDINA |